top of page

In 1972, on a quest to find the perfect packaging for a sphere, inventor Robert Burdon (RB) discovered, independently from Archimedes, the rhombic dodecahedron. He then went on to design and build a skeletal version of a rhombic dodecahedron model incorporating a hexagonal, common nodal design, with six bearing journals to which the rods ends were attached and free to pivot. Although not a stable structure, it did display a disciplined geometrical folding movement, which allowed the structure to assume a variety of different geometric shapes. RB christened this device the “Widget Toy” and he commissioned a prototype to be modeled. During a play session with his young daughter, the toy fell to the floor and quite by serendipity, assumed an unusual folding configuration that was later recognized in 1991 by Professor H. Nooshin, Director of the Space Structures Research Centre of the University of Surrey in the UK, as a discovery of a new partial tensegrity truss. RB named it the Nodular Octahedral Double-Layered, Expandable Truss, (What is a NODLET?) and a Short Report was published in the International Journal of Space Structures, Volume 6, No 1 in 1991.
​
​
​
​
​
HISTORY
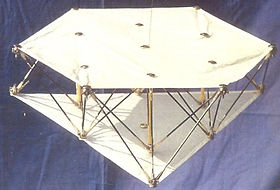
Excited by his discovery and convinced that the direction in which to concentrate his focus would be aerospace, RB moved to Hawaii, USA where he met a fellow ex-pat David Hayter, a graphic designer and marketer. Together they formed a company called Structure Development, filed a provisional patent application, and set out to find interested parties in the aerospace community.

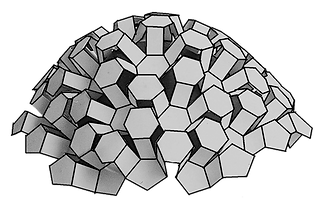
There was a lot of talk around this time about Nasa's proposed space station, and consequently their first contact was with the people who were making the decisions. Little did they know, but the decision regarding the makeup of the station, ie a platform on which modules are attached which was what they were proposing, vs individual modules connected by an exterior framework had been made many years earlier. This was the first of many disappointments culminating in the patent application expiring and the high hopes for the NODLET concept dashed.
​
​
​
A few years later, while working on a way to model the capabilities of a collection of Nodlets, another discovery was made. RB realized that they were no longer looking at a truss, and it had, in fact, morphed into another geometric form - that of a pseudo-honeycomb which they called HEXAFLEX. Excited by this new discovery they went on to file a patent application and were rewarded with its issue on January 18, 2007.

Their initial investigations into honeycomb led them again to NASA - this time to their X-33 spaceplane demonstrator, which was on the verge of being canceled, due in part to delamination of the skins forming the composite panels which made up the huge fuel tanks. Their hope was that by introducing HEXAFLEX to the project team, they could maybe help salvage the program, and in turn gain validation of their concept. Sadly the X-33 project collapsed before HEXAFLEX could be of any use. ​
Undaunted, the two went on to explore other avenues where honeycomb was being used and came to realize the enormous potential for a new type of core that could possibly replace or augment the existing state of the art: ​
ABSORPTION PROTECTIVE STRUCTURES - energy absorbers/bumpers, crash test barriers, flexible body armor, ballistic shields
AEROSPACE - Composite panels, dirigibles, flaps, ailerons, struts, radomes, doors, rudders, flooring, cowlings
AUTOMOTIVE - door and roof panels, fairings, heat exchange panels, double-skinned exhaust manifolds, flexible fuel tanks
CONSTRUCTION - wall panels, false ceilings, roof panels, flexible tubular structures, 3D Printed concrete structures
MARINE - hulls, decks, bulkheads, stringers, covers, hatches ​
MISCELLANEOUS - double-skinned storage tanks, oil pipelines, soil stabilization mats, solar energy panels, sound attenuation panels RAIL - doors, floors, ceilings partitions
RECREATION INDUSTRY -Snowboards, Wake Boards, surfboards, athletic shoes
MEDICAL - Nanotechnology, capsids, inter-cellular matrix, medical stents, surgical mesh ​
​
​
More recently they have come to realize that the best way to manufacture HEXAFLEX, using a variety of different materials, is to use 3D printing. Additive Manufacturing (AM) is an important technology innovation with roots that go back nearly three decades. As recently as August 2015, it was announced by MIT that they had designed a 3D printing device that could incorporate up to 10 materials concurrently. This could well be the first of such machines that employs cutting edge technology to advance manufacture all kinds of things. NASA is on board with the 3D printing phenom with plans to use the technology in orbit, and also future manned missions to Mars where sustainable habitat is vital. ​
They have had many years in which to envisage possible uses and applications for HEXAFLEX. Most of these ideas are theoretical, but this is the first time in their history that by using 3D printing technology, they are able to build prototypes and samples that convey the ideas and bring them to life. The future is exciting. With 3D printing fast becoming a legitimate manufacturing platform, and machines being developed that can print multiple materials concurrently - a concept completely in sync with the HEXAFLEX system, it remains to be seen where it will fit in, and which applications will be among the first to find a viable and sustainable market.
​
​
​
​


bottom of page